Among the cast materials used for linings are Ni-Hard. chrome-molybdenum steel, and manganese steel. Rolled alloy steel plate with lifter bars is available Rod mill liners are subjected to severe impact. Premature breakage and scrap loss are reduced by correct selection of liners for the specific gnnd-mg duty. Additional benefit results from use of a backing material, such as rubber between the liners and the mill shell.
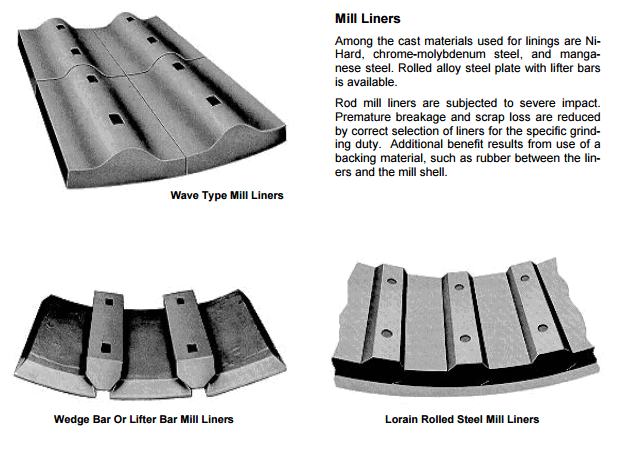
Without the cushioning effect of the ore, the impact of the tumbling rods can break a rod mill liner especially if the force is concentrated at one spot. If the load comes down on a small piece of rod or other hard object such as a bolt or nut that happens to be on a worn or weak liner. The entire weight of the rod or rods will be transferred to that spot. The result may be a broken liner. Of course the condition of the mill liners will be a major factor in its survival.
Even if the liner doesn’t break, the impact will begin to loosen the bolts that hold the liners in. Once these bolts are loose they will begin to leak. Leaking bolts on a mill can cause damage to other equipment by getting dirt into motors or gears, and at the very least they cause a mess to be cleaned up.
There are three basic types of wet tumbling mills. They are, ROD MILLS which we just finished discussing, BALL MILLS, and AUTOGENOUS MILLS. The Ball mills are much like the Rod mills except that they use balls as their grinding media. The size of these balls may range from three quarters of an inch to over five inches in diameter. There is a definite difference in the grinding performance between a Ball mill and a Rod mill. The Rod mill has a higher impact force than a Ball mill. This makes the Rod mill better suited to grinding courser or harder ore. In contrast the Ball mill is more effective in producing a finer grind. In most mines, where there is more than one mill grinding the ore, as in the case of our third and fourth schematics. You will find the first mill to grind the rock, sometimes referred to as the PRIMARY GRIND, will be a Rod mill. The SECONDARY GRIND will be a Ball mill. In some cases if the work index of the ore is low enough the primary grind maybe a Ball mill as well.
The difference between primary and secondary grinding mills is in the design of the liners and the size of the grinding media. The primary grind requires a higher lift to get the impact necessary to reduce the size of the ore.
A secondary mill will require the high surface contact with more of the grinding motion that the lower cascade brings. This means that the secondary mill will have LOW PROFILE ROD MILL LINERS in them. If it is a ball mill being used as the primary grind the size of the grinding media will be increased, this is to increase their impact. A HIGHER PROFILE LINER may also be used. The two variables, the high surface contact and the greater impact will be balanced, to produce the cheapest and best combination.