Table of Contents
Pyrite has long been used as a source of sulphur, and its recovery as a by-product from the flotation of certain base metal ores is a well established practice. Large tonnages of mill tailings which have accumulated as a result of various milling operations frequently contain significant amounts of pyrite. In many instances these tailings can be treated to yield pyrite concentrates that are a suitable source of sulphur dioxide for the manufacture of sulphuric acid. Such concentrates must normally contain at least 48% sulphur.
The Pyrite Tailings Flotation Circuit Flowsheet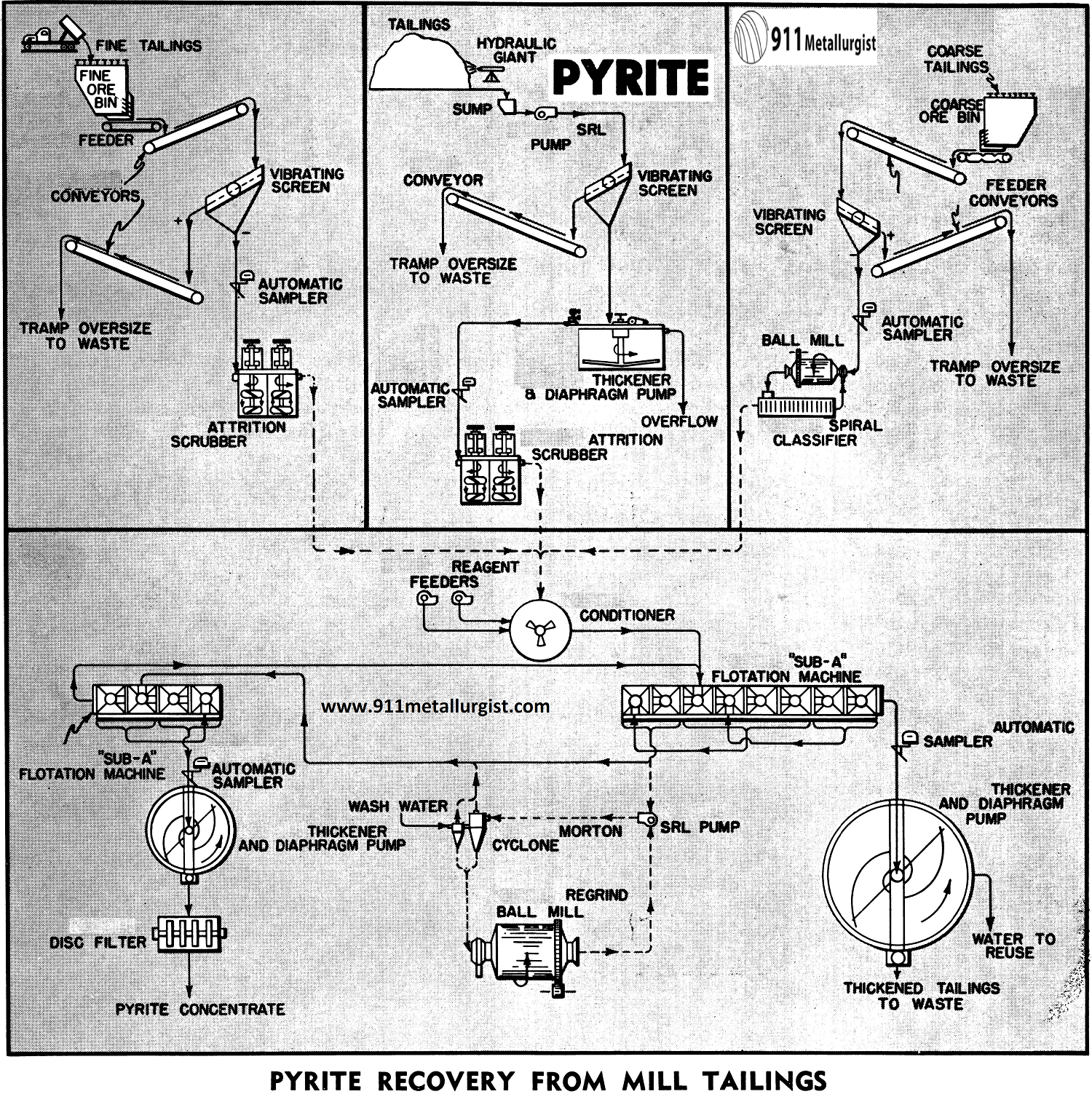
Initial treatment of the tailings preparatory to pyrite recovery depend upon the source and particle size of the material to be treated. Fine material, such as flotation tailings, normally does not require size reduction prior to pyrite flotation. On the other hand, coarse tailings such as those produced from certain gravity concentrating operations, must be ground to provide a product suitable for flotation. This study deals with various types of tailings and subsequent treatment methods.
FINE TAILINGS
Fine tailings may be either mined dry and transported to the mill by truck or they may be mined hydraulically and the resulting pulp pumped to the mill. In either case the tailings should be screened prior to treatment to remove tramp oversize and debris.
The surfaces of pyrite contained in old mill tailings are frequently oxidized to such a degree that recovery by flotation may be difficult. Hence, removal of the oxidized films may be necessary in order to achieve satisfactory recovery of a pyrite product with acceptable purity.
Removal of the oxidized surface films is most effectively accomplished by scrubbing at densities of from 70-80% solids in a Attrition Scrubber. This machine is equipped with specially designed rubber covered turbine type propellers which promote an intense inter-particle scrubbing action which removes the undesirable oxidized coatings from the pyrite. Tailings which are mined dry may be diluted with water to the proper consistency for scrubbing. Hydraulically mined tailings normally require thickening to remove excess water prior to the high-density scrubbing.
COARSE TAILINGS
Tailings in which the pyrite is not free from the associated minerals or, which is too coarse to be handled by flotation as mined, must first be reduced to the proper particle size by grinding. This is accomplished in a Steel Head Ball Mill in closed circuit with a Spiral or Rake Classifier.
CONDITIONING
The scrubbed tailings, or the classifier overflow from the grinding circuit as the case may be, flow to a Super Agitator and Conditioner where reagents are added to activate the pyrite. For this purpose a xanthate or dixanthogen type collector is normally used. Since pyrite generally responds most satisfactorily to activation in an acid circuit, sulphuric acid in a quantity sufficient to produce a pH of 6 or below is also added to the conditioner.
FLOTATION
From the conditioner the pulp flows to a “Sub-A” Flotation Machine. The cells are arranged to provide for roughing, scavenging and one stage of cleaning, and then final cleaning. The scavenger froth is returned by gravity to the second rougher cell for retreatment. The rougher froth flows to the first- stage cleaner cells. If middling particles are present the froth from the first-stage cleaner cells is reground in a Regrind Ball Mill operating in closed circuit with a Morton Cyclone Classifier. The classifier overflow then is pumped to the final flotation cleaner cells. Since the final cleaning of pyrite may be carried out at a pH of from 6.5 to 7.0, lime may be added to the regrind circuit to neutralize the excess acid, thus avoiding the expense of having acid-proof equipment in this part of the flowsheet.
Final cleaning normally consists of two stages with the cleaner tailings being returned to the head of the rougher flotation circuit.
THICKENING AND FILTERING
The cleaned pyrite flotation concentrate is pumped to a Spiral Rake Thickener to remove excess water prior to filtering. A Adjustable Stroke Diaphragm Pump, mounted on the thickener superstructure, meters the thickened pyrite to a Disc Filter. Since the filter is often operated only at fixed intervals, sufficient thickener capacity is provided to adequately store the concentrates accumulated during filter shut-downs. The Adjustable Stroke Diaphragm Pump is used for recirculation of the thickened solids during such periods.
Where water must be reclaimed for re-use, the rougher flotation tailings are thickened in a Spiral Rake Thickener and the plant water is reclaimed.
SAMPLING
Possible variations in the feed require reliable sampling for efficient mill control. Automatic Samplers are used on the heads, tailings and concentrates.
Summary
Although the flowsheet described in this study is designed specifically for the recovery of pyrite from old mill tailings, it can be, with certain modifications, the basic treatment process applicable to the recovery of other minerals from tailings.
LABORATORY TESTS
The economics of processing tailings depends on many factors which are apt to vary throughout the tailings deposit. Therefore careful and extensive sampling of the tailings deposit is essential. Small-scale batch tests should be followed by pilot mill tests to assure that the mill has the flexibility to meet the changeable composition of the mill feed. Since one mill will often handle tailings from several dumps in the area a complete knowledge of all deposits is necessary so that adequate blending facilities and flexibility of flowsheet may be incorporated in the mill.
Attrition Scrubber removes oxidized surface films.
Source: This article is a reproduction of an excerpt of “In the Public Domain” documents held in 911Metallurgy Corp’s private library.